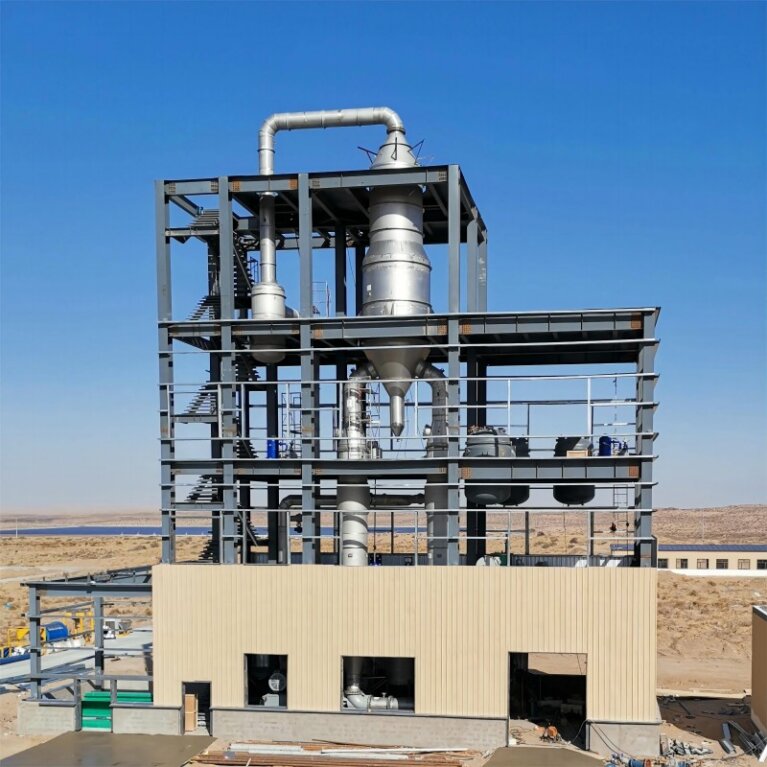
MVR Heated Distillation
MVR heated Rectification technology
Working Principle:
The gas phase steam at the top of the distillation column is compressed by the MVR compressor to obtain the high temperature and pressure, which is used to heat the kettle liquid. After-heat of the steam is then recovered and utilized, so that the distillation system is completely self-circulating.
The main equipment of the process are:
- rectify column
- re-boiler
- MVR compressor
- condenser
- tanks and pipes
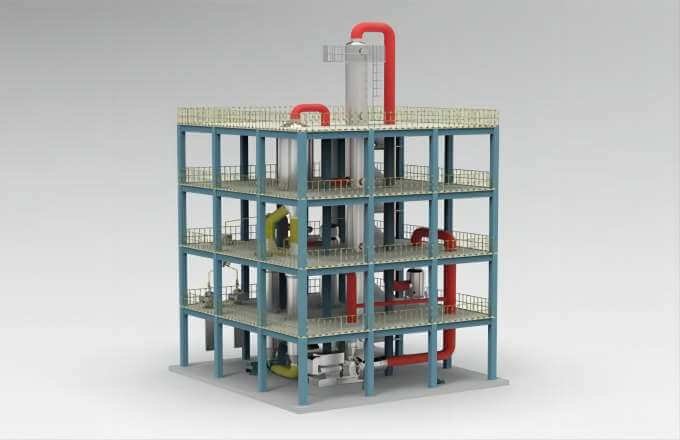
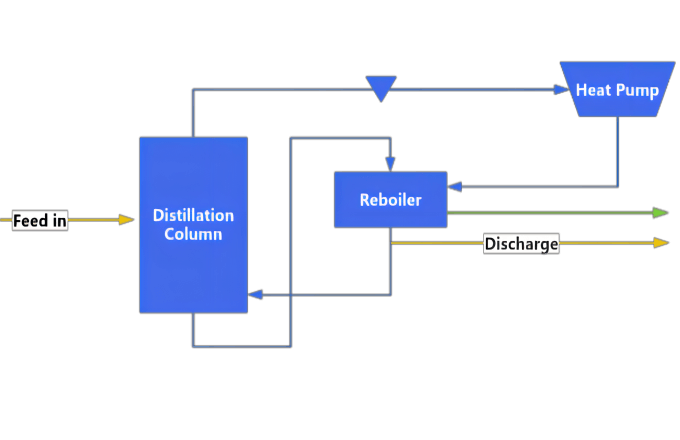
About MVR Compressor in MVR heated Rectification
Heat pump is the core device in the MVR heat pump distillation technology. It increases heat energy from lower temperature to higher, at the cost of consuming a certain amount of mechanical work. The heat pump for rectification is to pressurize the low-temperature gas with a compressor, raising the temperature, when overheated, the gas can serve as the heat at tower bottom. The circulating medium of heat pump absorbs heat of the steam at tower top in the condenser and then evaporates as gas. After compression, the gas is heating up and then enters the re-boiler to condensate. The condensate liquid passes through the throttle valve and flows into the condenser to be evaporated.
Typical Cases in Sanfeng Tech
Take below parameters in Sanfeng for example:
Medium: DMF
- Feed in: 5.5 t/h
- Reflux: 1.5 t/h
- Column Top Out: 3.5 t/h
- Column Bottom Out: 1.75 t/h
- Motor power: 560 kw
Before VS After:
Economic benefits: 10,690,000 CNY – 2,506,000 CNY = 8,184,000CNY
That’s what saved by adopting our MVR Heated Distillation!
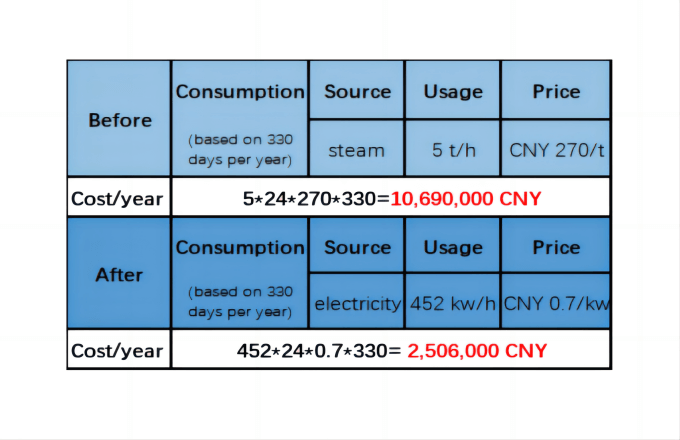
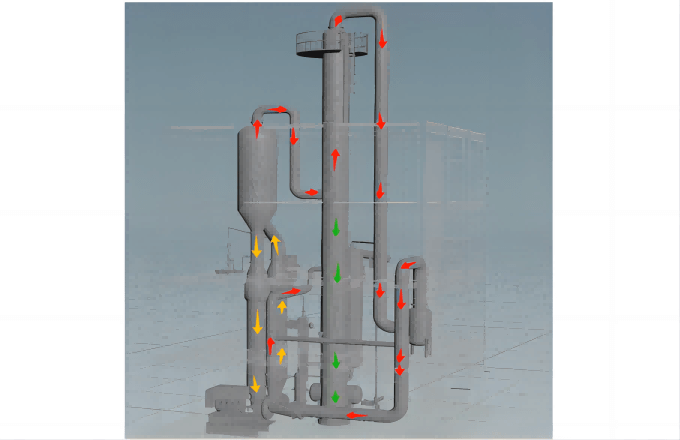
Advantages of MVR Heated Distillation
- High efficiency &energy saving
- Heat transferred from low temperature medium to high throughthermodynamic inverse process
- Improve the efficiency of the separation process
- Solve the problems of traditional heating method: energywaste and equipment loss
- It usesheat pump to drive the compressor to heat the steam and then compress and release energy.
In the distillation process, the heat pump technology can transfer the heat from the evaporator to the condenser, thus realizing the effective use of heat energy. It reduces the maintenance cost, improving the service life of equipment. The system is automatically controlled, so that it can realize the reasonable allocation of energy according to the process requirements.
Problems may happen during the distillation process
- Flooding: The foam layer on the tower plate can be lifted to the top of the down-flow spout. The liquid on the plate cannot flow down smoothly, leading to the obstruction of the liquid flow, resulting in “Flooding”.
- Back-mixing: When the rising gas is a liquid on the tower, high liquid and low liquid are mixed together, destroying the concentration change of the liquid along the flow direction.
- Liquid leakage: In the operation, if the uprising gas doesn’t have enough energy to pass through the liquid layer on the tower plate, it cannot hold the liquid, resulting in liquid leakage.
- Entrainment: In the process of mass transfer, plenty of entrainment will bring the heavy component that should not be up to the tower top into the product.
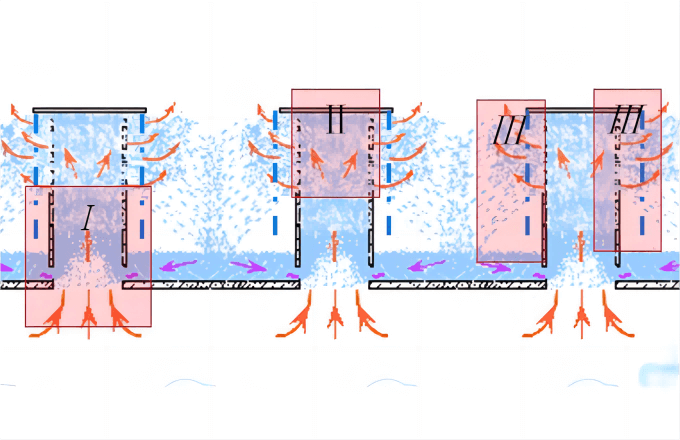