ZLD Drying System
What purposes can the ZLD drying system realize?
With the constant operation of our MVR/MEE evaporation system, negative impacts enrich, getting in the way of:
-
-
operation cost reduction
-
continuous high-quality valuable salt production
-
ZLD
-
To provide our client with an efficient MVR/MEE evaporation system & realize the above objectives, the following ZLD drying systems are usually introduced:
I. Drum dryer
II. Vacuum low-temperature drying system
III. Rake dryer
IV. Steam kettle dryer
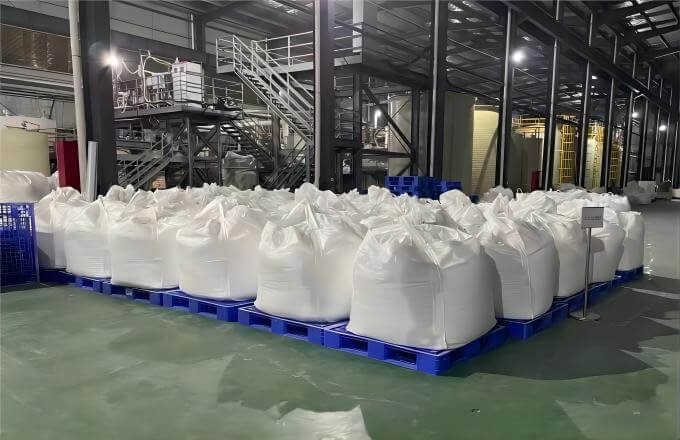
I. Drum dryer
Introduction
The most usually adoption is the drum dryer. Combining wet evaporation with drum drying technology, the drum dryer is a kind of inner heating conduction dryer, equipped with a rotating drum and a scraper.
It is always adopted for further moisture content reduction, such as discharged mother liquor from MEE or MVR evaporation systems.
Function detail
Step ①. The feed is pumped into the feed tank at the bottom of the dryer.
Step ②. Contacting the wet feed, the drum rotates just on the top of the feed tank, with the feed attaching to the drum surface forming a thin film.
Step ③. The dehydration is conducted by the hot air delivered to the drum’s inner wall, then conducted to the outer wall of the drum, and then transmitted to the feed film.
Step ④. The scraper attached to the surface of the drum removes the dehydrated feed to a spiral conveyor placed below the scraper, through which the dry crystal is collected and packed.
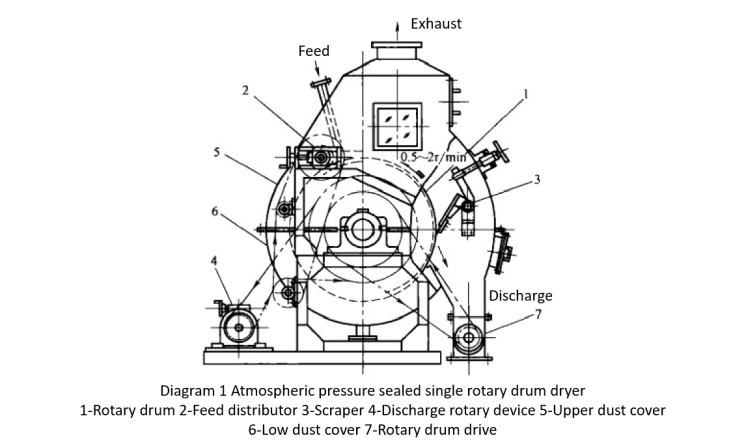
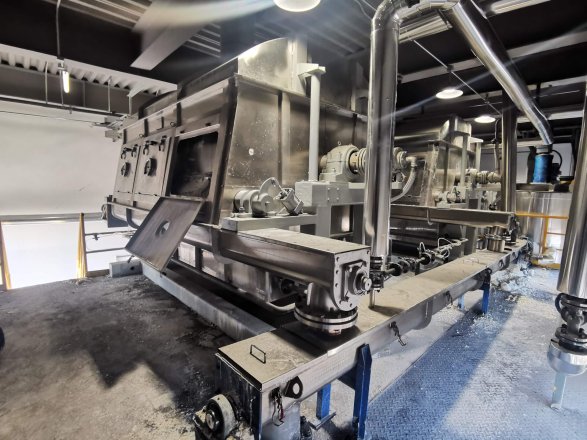
Applications
The drum dryer can be adopted in the product drying of:
- Chemical, mining, metallurgy (ore, slag, coal, metal powder, clay, diatomaceous earth, kaolin)
- Agriculture, feed, fertilizer(straw, grass, leaves, fish meal, corn paste, starch residue, wine lees, medicinal residue, fruit residue, soy sauce residue, bagasse, grass char, organic compound fertilizer, sludge, aquatic product waste, food factory waste, slaughterhouse waste, organic fertilizer, inorganic fertilizer, phosphate fertilizer ammonium sulfide)
- Other powder and granular materials with special requirements (a variety of crystals, light calcium carbonate, active clay, magnetic powder, graphite, inorganic mud, clay, lime slurry, ore mud, phosphorus slag, aluminum plant red mud)
The feed:
The drum dryers are normally used to treat liquid or slurry materials featuring:
-
- high moisture content,
- high and complex salt content,
- high organic content,
- high viscosity,
- high boiling point rise.
Advantages & disadvantages
Advantages:
-
Lowing the investment cost
① Automatic operation & less labor consumption,
② Its feed features a vast viscosity range,
③ No residual, small yield treatment can be carried out,
④ Easy to clean. The feed can be changed easily,
⑤ Require no dust collection equipment.
-
Guaranteeing the product’s economic value
① Uniform quality products,
② High thermal efficiency (up to 70%~80%),
③ Swift dehydration rate.
Disadvantages:
① A relatively low dehydration effect,
② Low yield capacity.
II. Vacuum low-temperature drying system
Introduction
Combining thermal conduction and blades stirring, the vacuum low-temperature drying system operates with a vacuum chamber equipped with a thermal conduction jacket containing heating medium.
Function detail
Step ①. The feed is fed from one side of the dryer, stirred, and pushed towards the other end by the even-distributed multi-layer scrapers fixed on a center-placed horizontal spindle.
Step ②. The heating hollow jacket covering the dryer’s shell contains the heating medium. By thermal conduction, it heats the feed with a relatively low temperature(normally 32 ~45℃).
Step ③. The dehydrated feed is discharged at the other end, while the exhaust is separated, cooled, and collected from the separator at the top.
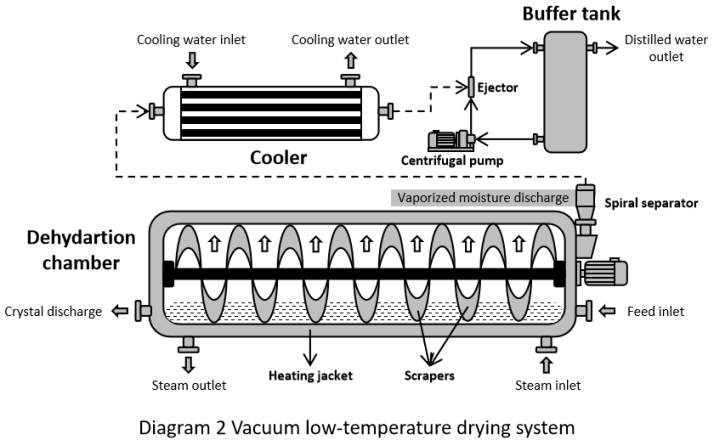
Application
It can be adopted in the production of:
-
- pharmaceutical
- chemical product
And also, it contributes a lot of effort in ZLD, treating:
-
-
dialysate
-
printed sewage
-
salt slurry
-
mother liquor reverse osmosis treatment
-
mother liquor for MVR/MEE system
-
Advantages & disadvantages
Advantages
-
Lowing the investment cost
① Low operation noise
② Low energy consumption
③ Small footprint
④ Automatic & continuous operation
-
Guaranteeing the product’s economic value
① High operation efficiency
Disadvantages
① High equipment cost
② Difficult to maintain
III. Rake dryer
Introduction
As a vacuum indirect thermal transfer dryer, its inner wall is equipped with a jacket for heat conduction.
Inside the dryer, the horizontal rake agitator is fitted with cast iron or steel-made blades fixed on a square or circle axle, distributed evenly on both sides.
To ensure the drying effect, the equipped reduction drive and an automatic steering device change the agitator’s rotation direction every 5~8 minutes.
Function detail
Step ①. The wet feed feeding at the inlet located on the top of the dryer shell,
Step ②. The feed is stirred and painted on the inner shell wall, where it is heated, and removed from it continually,
Step ③. The vaporized moisture is pumped away in time by the vacuum pump.
The high operating vacuum degree boosts the thermal movement of the moisture molecules in the feed, facilitating the dehydration effect.
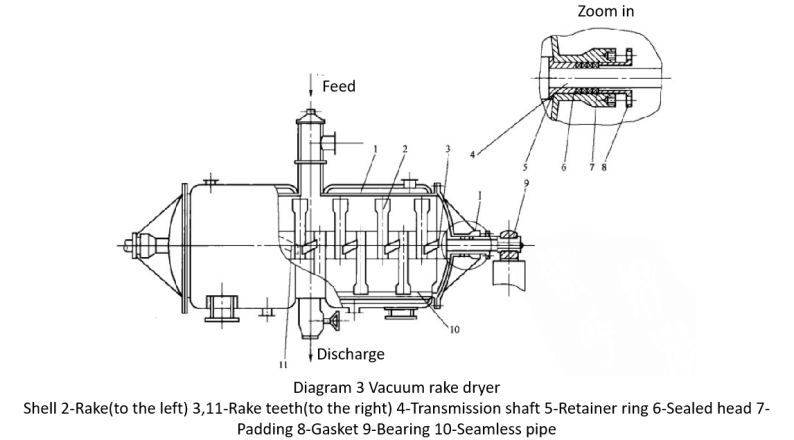
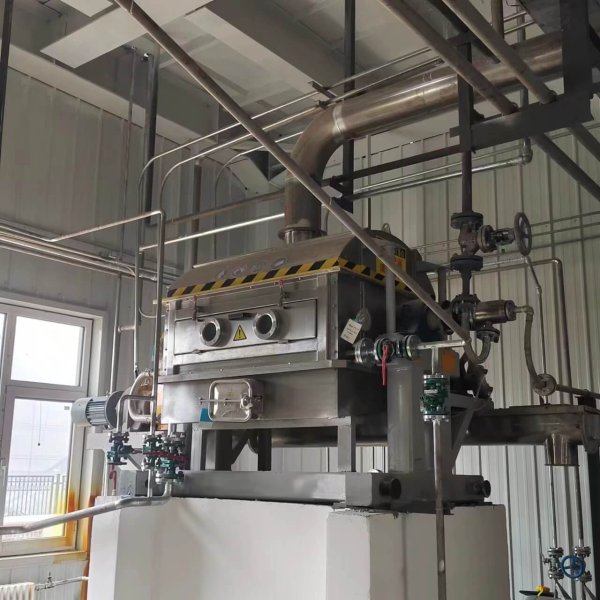
Applications
As the vacuum rake dryer generates the power shaped discharge which can be packed directly without crushing process after drying.
It is widely adopted in the production of :
-
- pharmaceutical (produce granules, powder, capsules, etc.)
- food (produce dried fruit & vegetable products, milk powder, dried meat floss, etc.)
- chemical products (produce solid alcohol products, such as sodium lauryl sulfate & potassium lauryl sulfate.)
The feed:
With indirect heating and vacuum discharge, this device is suitable for drying slurry or paste materials, with 15%~90% moisture content, featuring:
-
- small quantities,
- thermal sensitivity,
- oxygen sensitive,
- easily oxidized,
- easy to scale,
-
explosive.
Advantages & disadvantages
Advantages:
-
Lowing the investment cost
①Small steam consumption,
②According to the feed, the selection between packing seal and mechanical seal ensures a good sealing effect & long service life,
③Easy operation. Low manpower consumption,
④Environment friendly. Less feed leak.
-
Guaranteeing the product’s economic value
①Strong adaptability, with a relatively wide application,
②Sound yield product quality, thanks to the feed stirring avoiding overheating, and accelerating dehydration.
Disadvantages:
① Complex structure & expensive fabrication cost,
② Low yield in each discharge, intermittent operation & long drying process time,
③ Due to the incomplete material discharge, it is not convenient to change the production variety frequently,
④ Frequent maintenance and overhaul of the dryer must be carried out, to maintain the vacuum degree.
IV. Steam kettle dryer:
Introduction
The steam kettle dryer is equipped with a single kettle, with a hollow jacket containing a heating medium covered outside, and an agitator standing vertically inside.
Function detail
Step ①. Discharged from the evaporation system, the feed is pumped into the dryer from the top inlet.
Step ②. Simultaneously, the secondary steam from the evaporation system is injected into the jacket for the heating efforts, with its condensate discharged from the outlet at the bottom.
Step ③. The stirring effort boosts the dehydration efforts, with the separated moisture discharged via a vent system
Feed:
Usually, its feed features:
-
- loose,
- paste,
- adhesive materials,
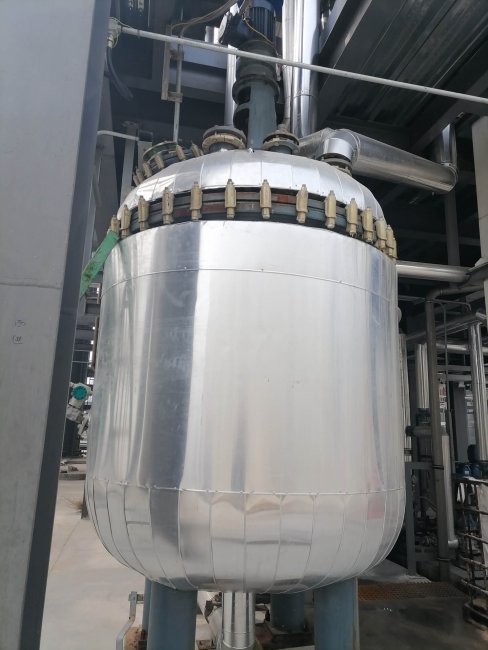
- Applications
It is widely adopted in the application of massive drying productions, such as:
-
- foods (vegetables, fruits, grain),
- chemical (reaction, distillation, evaporation),
- pharmaceutical (High-temperature sterilization, drying, tablet pressing, granulation),
- drying of wood and papermaking.
For the purpose of ZLD, it can process:
-
- filter-cake,
- discharged mother liquor from multi-effect evaporation,
- landfill leachate.
Advantages & disadvantages
Advantages:
-
Lowing the investment cost
① eco-friendly & energy conservation,
② wide range of application,
③ easy control,
④ massive yield capacity.
-
Guaranteeing the product’s economic value
① high drying efficiency,
② swift drying.
Disadvantages:
- high operation cost,
- high-quality requirement on the heating medium steam,
- frequent equipment maintenance.