Drying and Granulation System
What purposes can the drying and granulation system realize?
Currently, the evaporation and crystallization system is widely adopted treat wastewater with large volume, complex water quality and high pollutant concentration.
After the treatment of evaporation, the generated valuable salt product can be packed as a beneficial product for sale, earning the investor a sound profit.
What kind of devices service you on this matter?
When we receive the discharged crystal product from the evaporation system, it takes two steps to generate the salt product:
Step 1 Dehydration & Granulation
The following devices can serve you in such demand:
I. Vibratory fluidized bed dryer
II. Boiling fluidized bed dryer
III. Spray dryer
Step 2 Packing
IV. Packing unit
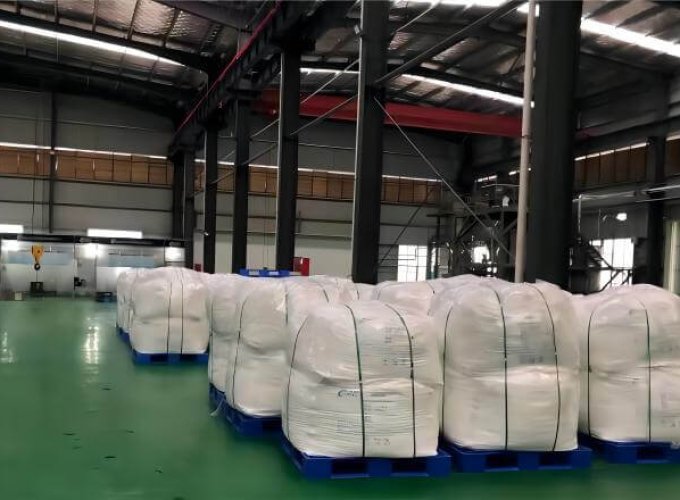
I. Vibratory fluidized bed
Introduction
The vibratory fluidized bed (diagram 1) takes advantage of the flowing material, tossing the fluid to set it into a loose status via vibration, to realize the low bed fluidization effect.
Severing as a modified drying unit, the vibratory fluidized bed operates with additional vibration effects, based on the normal fluidized bed.
It also can be adopted as the secondary drying/cooling equipment, combining with the spry dryer or boiling fluidized bed dryer.
Function detail
The vibratory fluidized bed operates not only with the vibration alone but also with the assistance of the hot air flowing in the system:
Step ①. Wet feed feeding. The vibration ensures its even and continuous flow.
Step ②. Air injection, filtration, and heating.
Step ③. Air distribution and injection into the air chamber at the bottom of the dryer.
Step ④. Heat and mass transfer between the feed and the hot air bubbling from the bottom of the fluidized bed through the air distribution pore plate.
Step ⑤. Exhaust collection at the top of the dryer to recover entrainment.
Step ⑥. Dehydration is complete, followed by the product collection and packing procedure.
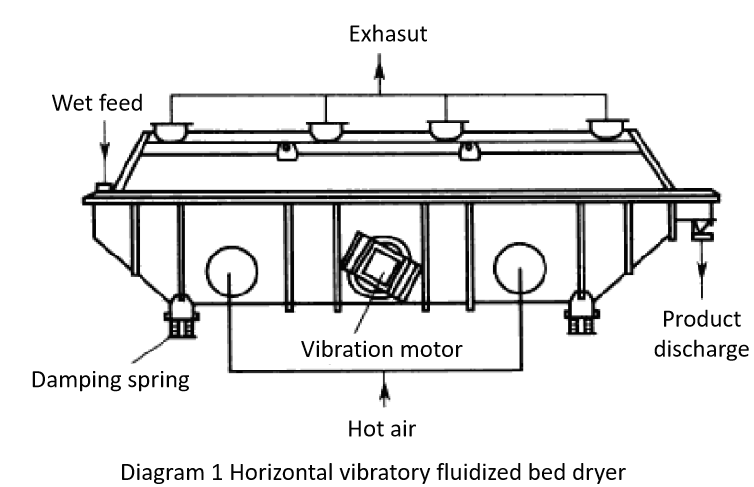
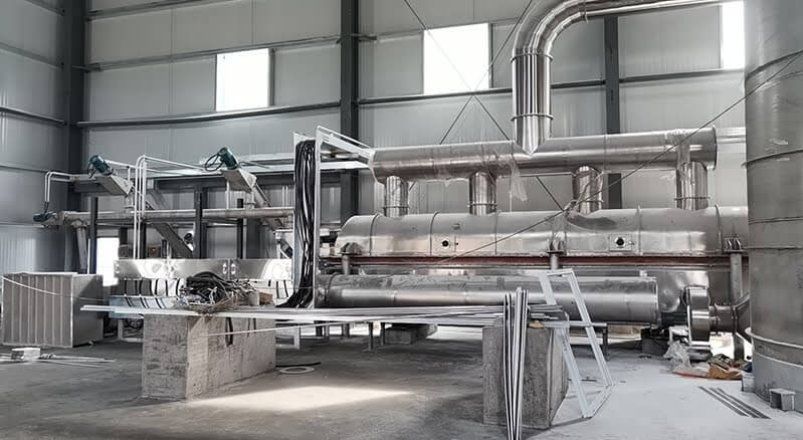
Applications
The vibratory fluidized bed vigorously engages in the production of following products:
-
- Pharmaceutical (drying, mixing, granulating, coating, smashing, sieving, etc.)
- Food (drying, cooling, conveying, classification, etc.)
- Chemical (compounding, reaction, purification, crystallization, and separation)
- as well as, electronics, ceramic, glass, building materials, and etc.
It also provide eco-friendly solutions such as:
-
- wastewater treatment
- solid waste incineration treatment
Advantages & disadvantages
Advantages:
- Lowing the investment cost
①Low air consumption and entrainment discharge;
②Require small volume or even without the exhaust collection system;
③Particle dehydration and classification can be realized simultaneously;
④Wide adoption, including powder or graininess feed;
⑤High heat usage efficiency and heat capacity coefficient;
⑥The vibration ensures an unblocking outlet.
-
Guaranteeing the product’s economic value
①The realization of the idealist fluidized bed;
②Vibration boosts the treatment of the particles featuring high moisture content and easy flocculation;
③Smoothly operation minimizes the broken and worn particles;
Disadvantages:
① The feed particle granularity must exceed 50~100 mm.
② The exhaust entrains a massive amount of material when the feed features a wide granularity.
③ Agglomeration may occur more easily when the particle features a high moisture content.
④ The non-spherical or viscosity feed will not reach an ideal fluidization state.
II. Boiling fluidized bed
Introduction
The boiling fluidized bed is also named as the horizontal fluidized bed dryer with single or multi chambers. Each chamber is equipped with adjustable vertical block plates and a hot-air inlet pipe below the pore plate for continuous processing.
Function detail
Step ①. The filtered and heated air is distributed through the branch pipes into each separated chamber.
Step ②. Through the flowing wet feed, the increasing volume of air injection accelerates the fluidization in each chamber.
Step ③. From the top, the exhaust discharge is processed through the cyclone separator, bag filter, and discharge fan.
The feed:
It is suitable to treat the feed featuring:
-
- wet and powdery
- sticky small block with large particles
- variable volume caused by the process (such as konjak, polyacrylamide, etc.).
Most of its feed features a 4~14 mesh loose granular, with 10%~30% moisture content before drying, and this content ended up with 0.2%~3%.
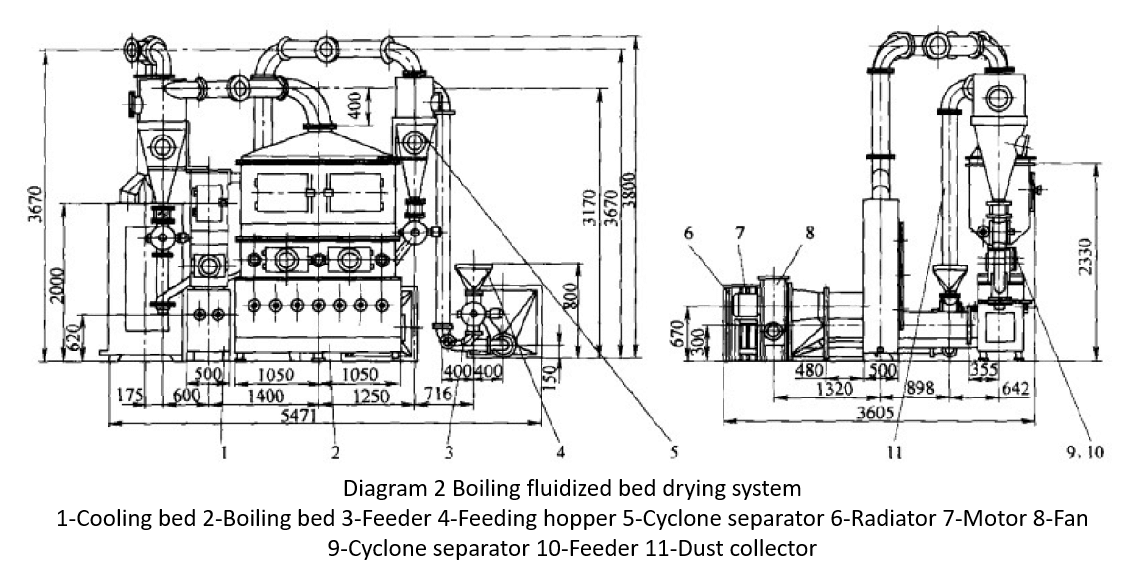
Applications
Its drying and granulation functions (such as screw extrusion, swing, or high-speed mixing) are widely adopted in
-
- pharmaceutical,
- food production,
- fodder production,
- chemical product production.
If the feed bears much smaller particles (with 80 to 100 mesh or even a larger granularity), the extension section needs to be set on the dryer’s top to reduce the entrainment loss from the exhaust.
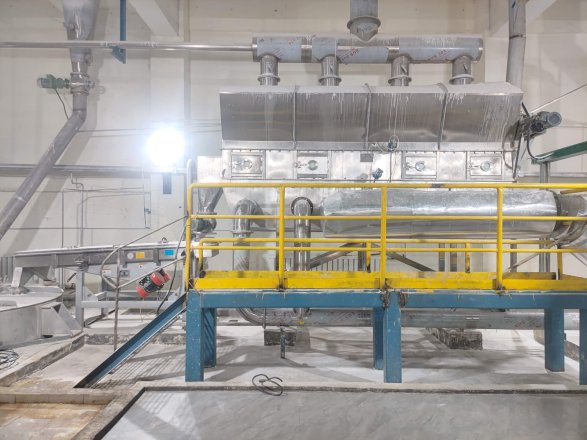
Advantages & disadvantages
Advantages:
-
Lowing the investment cost
①Simple structures facilitate easy fabrication, small footprint convenient discharge, and easy operation, as well as, high drying efficiency and more flexible production mode.
-
Guaranteeing the product’s economic value
①A relatively low operation temperature can be adopted for thermal-sensitive material treatment, without damaging the particles.
Disadvantages:
①When particles follow the fluid flow, it results in low heat & mass transfer efficiency.
②When particles move against the fluid flow, it requires more complex equipment, resulting in more investment costs.
③Different to control. Demand relatively strict operation conditions.
④Its height limitation controls airflow speed, to avoid drying effect reduction.
⑤Not suitable for the treatment of multi-variety and small-yield feed.
To overcome these disadvantages, normally, the following measures are adopted:
①The grid feeder adoption best ensures even feed distribution in the fluidized bed.
②The electric vibration feeder adoption boosts the fluidization effect, presenting a stable and smooth operation.
③The smooth inner wall with rounded corners can eliminate the dead zones, ensuring the dryer processes a better operation effect.
III. Spray dryer
Introduction
The adoption of the spray process allows the feed to form fog drop dispersing in the hot air. Taking advantage of the parallel-flow,counter-flow, or mix-flow, the full contact between the material and the hot air allows a swift dehydration.
The spray dryer can generate 30~500um particles without concentration, filtration, and grinding process in a short time, generally 5~30s.
Function detail
Step ①. Through the atomizer, the feed slurry turns into mist, encountering the high-temperature gas generated via the heated-gas supplier.
Step ②. With dramatic heat exchange, the mist turns into the pellet-shaped material as required standard within over or less ten seconds.
Step ③. The dried crystal enriches at the bottom of the drying tower and is discharged via a discharge pipe.
The feed:
The spray dryer is suitable for the treatment of solution, suspension, or slurry feed featuring high-temperature resistant, thermal-sensitive, and easy decomposition during the drying process, which can effectively improve product fluidity and instant solubility.
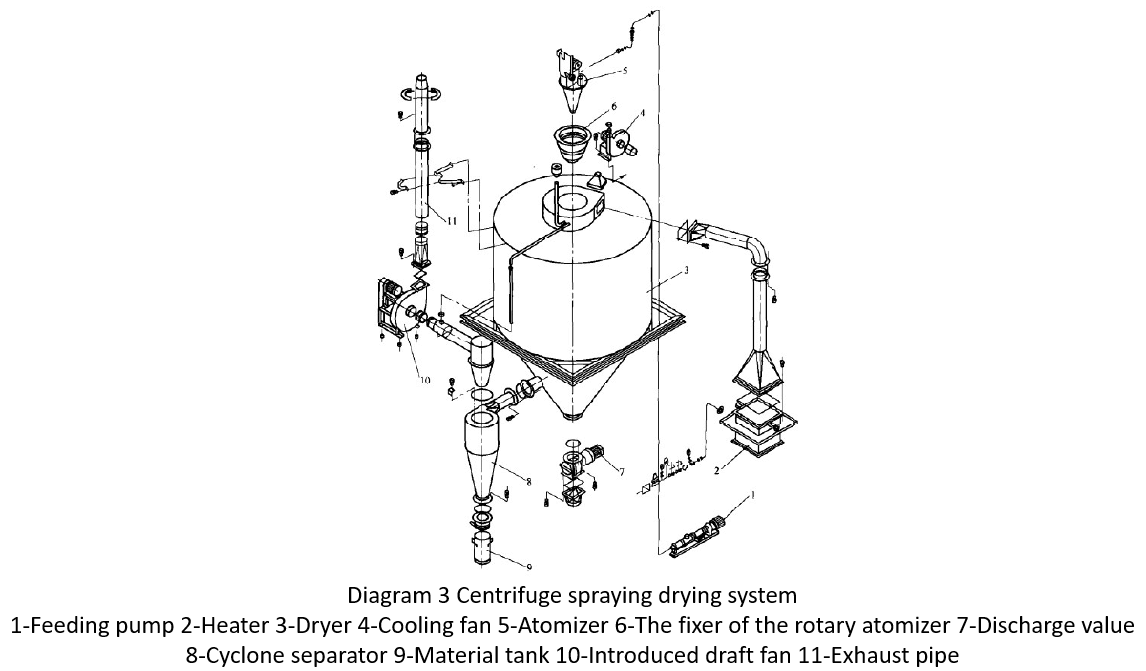
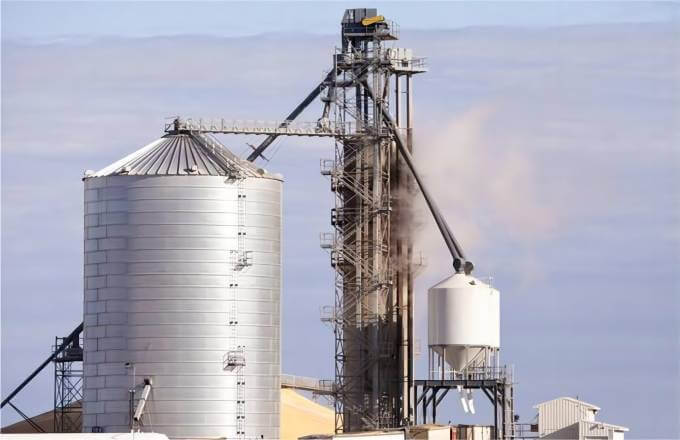
Applications:
- Flue gas desulfurization
- Pollution control & lignin products generation in paper-making black liquor treatment
- Pharmaceutical process acceleration.
Advantages & disadvantages
Advantages:
-
Lowing the investment cost
①Swift drying.About 95%-98% moisture can be evaporated instantly.
②Simply production process with convenient operation & control.
-
Guaranteeing the product’s economic value
①The generated product features a good uniformity, mobility and solubleness, with high purity and sound quality.
Disadvantages:
①Massive hot-air consumption requires huge subsequent processing devices, resulting in a high total fabrication cost;
②Not suitable for small yield application ;
③The nozzle is easily worn and blocked;
④High-viscosity feed is hard to be atomized;
⑤The relatively low volumetric heat transfer coefficient leads to a large device volume;
⑥Low thermal efficiency.
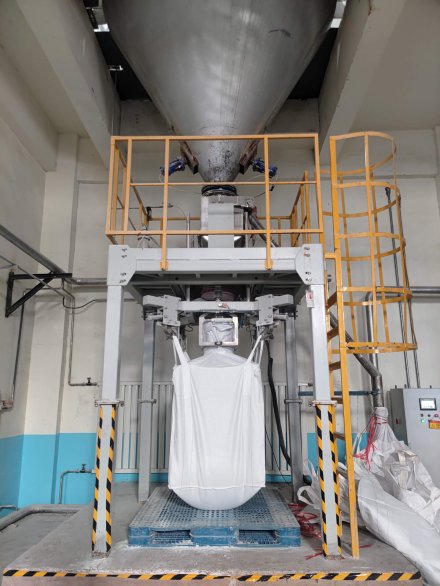
IV. Packing unit
The ton bag packing machine plays a multi-role, integrating electronic weighing and dust removal.
With less vulnerable parts, its high-accuracy packaging, practical structure form, and convenient operation boot its adoption in the packing of minerals, chemical products, building materials, grain, etc.
The semi-automatic quantitative packaging machine is extremely suitable for small granular and powdery scattered materials with good fluidity.
Its equipped superior weighing instrument ensures the accuracy, swift process, and high efficiency. And the automatic packing and unhooking demand no manual operation.
Now, the all-electronic semi-automatic quantitative industrial salt packing machine is widely adopted.
It can automatically operate the following procedures in an order:
- Staring with automatic bag blowing, the lifter lifts the bag in place where the product will be metered, discharged, and clipped.
- With the product filled in the ton bag, it will be conveyed to the position where the heat sealing will be placed.