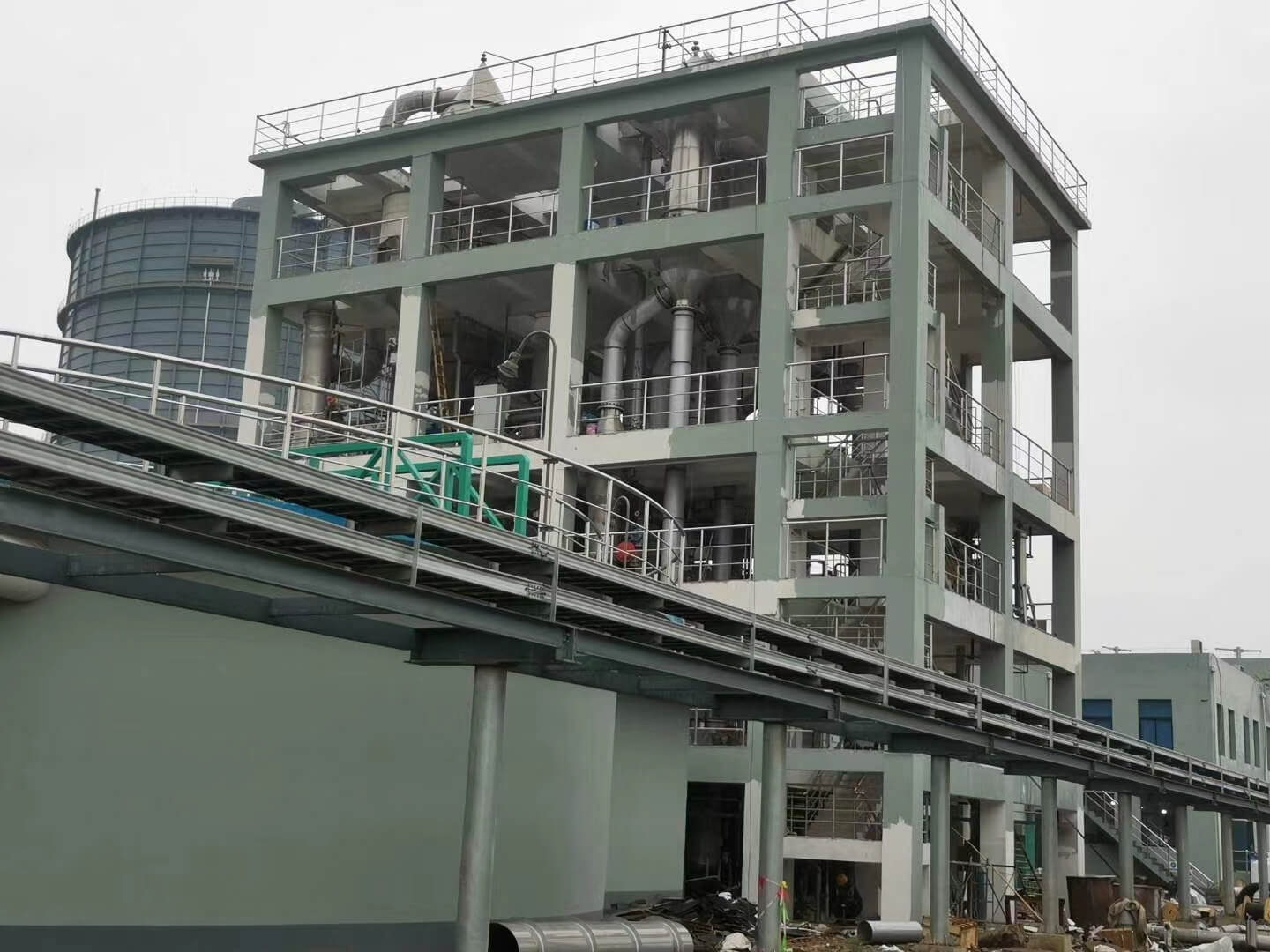
MVR Steam Compressor
What is MVR Steam Compressor?
Sanfeng Tech is one of the TOP manufacturers in China for the MVR Blower, with strong durability and easy maintenance.
MVR Steam Compressor is one of the key parts of the Mechanical Vapor Recompression Evaporation system to achieve the temperature and pressure increase of secondary steam. Compared with normal root compressors, Sanfeng’s centrifugal compressor has advantages like high efficiency, good stability, low noise, etc.
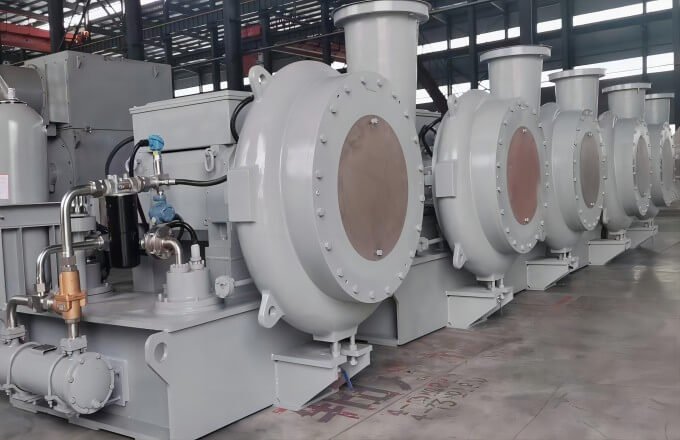
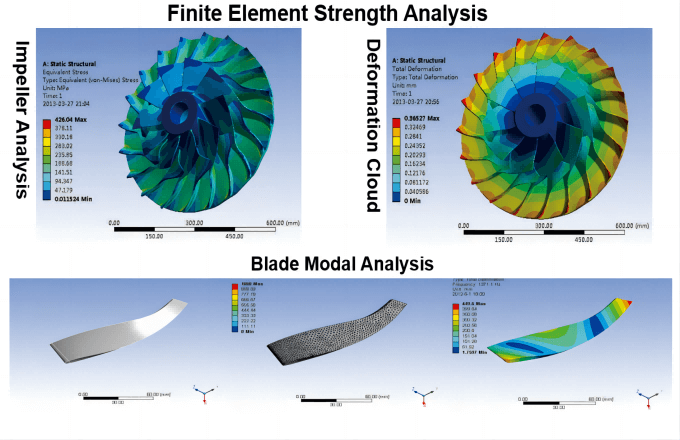
How the MVR steam compressor works?
Electricity to be converted to thermal energy through the steam compressor. The steam compressor is been drive by high speed motor. The secondary steam been suck into the steam compressor & then flow speed been increased by centrifuge force. After leaving diffuser, the steam pressure come down and automatically increase the temperature and pressure of steam.
Advantage of the MVR centrifuge compressor manufactured by Sanfeng
- Complete advanced manufacturer line for steam compressor from 3Ddesign, flow field flow analysis, impeller finite element analysis, rotor dynamic analysis and empty running test.
- Patent design for impeller connections which is called static friction connection had been designed for avoiding stress concentration to achieve long using life and stability.
- Automatic display can show more than 20 running data of steam compressor like bearing temperature, shaft vibration, motor temperature, exhaust gas pressure, oil pressure, spray liquid control, sealing control etc.
- Apply high speed motor direct drive system to reduce the consumption of gear box. Total efficiency can ensure at least 87%.
- Less space requirement, easy maintenance cost, low noise.
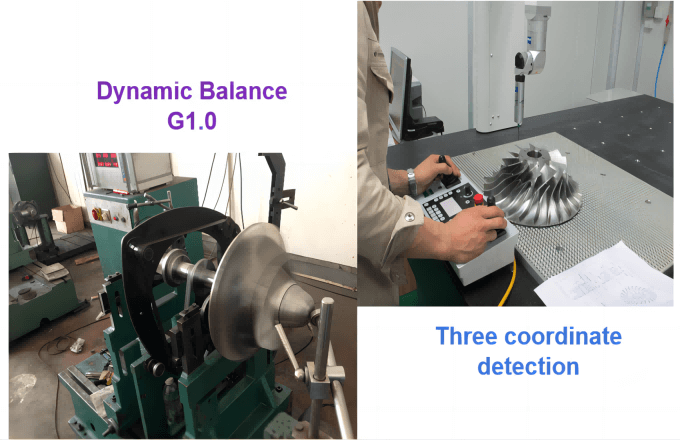
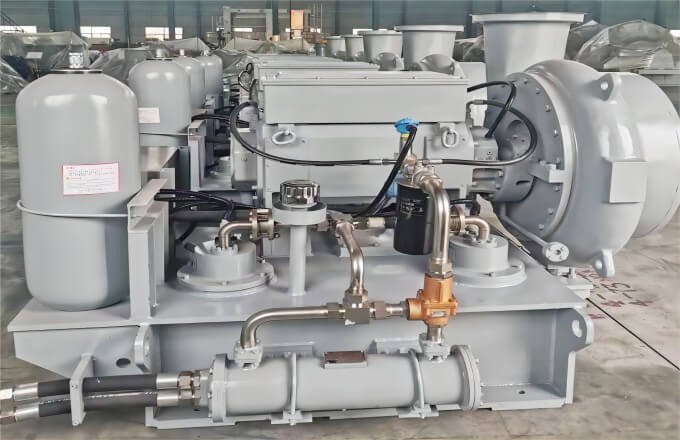
MVR steam compressor in Sanfeng Tech
Sanfeng Tech brings the state-of-art technology, depth experience, and applications knowledge to industries, with 65 years of designing, production, and upgrading advanced manufacturer facility, including the mechanical vapor compressor solutions for any MVR Evaporator or Crystallizer application for Water Reuse, Concentration, and Separation, Zero Liquid Discharge (ZLD), etc.