
Mother Liquor Drying System
About Mother Liquor Drying System
During evaporation operation in wastewater ZLD system, most of the wastewater is treated by suspended matter removal, impurity ion removal, reverse osmosis and evaporation crystallization, so as to obtain mother liquid with high solid content and clear liquid. The salt components in the mother liquid are discharged through centrifuge or pressure filter, the clear liquid returns the system to evaporate. COD in the evaporation system constantly increases.
But high COD not only affects the formation of crystallization grains, but also produces a large amount of foam in the evaporator, making the system unable to operate stably for a long period. Therefore, it is necessary to discharge the mother liquid from the centrifuge or the filter regularly. The discharged mother liquid with the drying system, form solid impurities, and finally help to achieve zero discharge of wastewater.
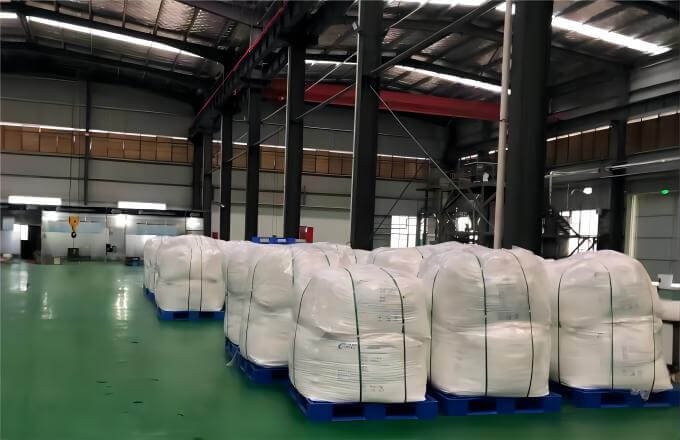
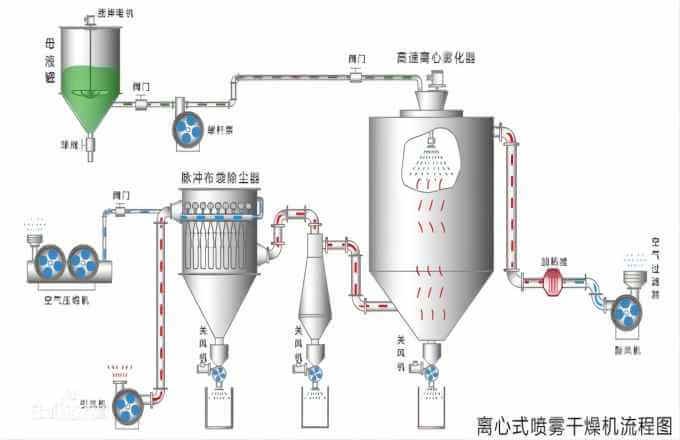
Technologies of Mother Liquor drying
- Spray drying
- Vacuum disc drying
- Scraper drum dryer
- Rake Dryer
- Steam kettle drying
- Spray drying:
Spray drying is a process of inhaling the material (solution, soliquoid or mash) through the nozzle into the drying cavity for atomization, where the solvent rapidly evaporates through the hot airflow, converting the small droplets into solid particles, and finally separating the air from the cyclone collector and collecting the dry particles. This technology has high requirements for material viscosity, density and impurity content.
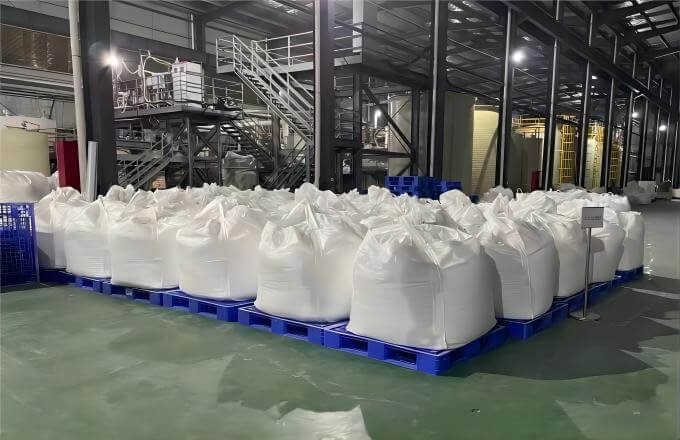
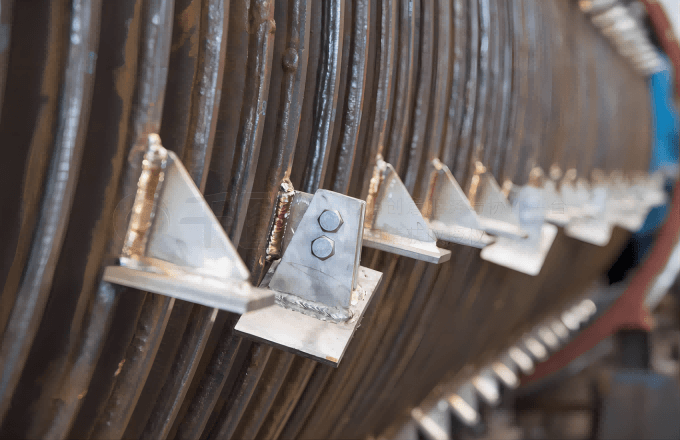
- Vacuum disc drying:
Vacuum disc drying is a process of sending heat carrier (hot oil, hot water or high compressed steam) into each layer of hollow disk, indirectly heating the wet material on the disk by heat conduction, under the mechanical action of rotary rake leaves, making the moving wet material evaporate at the operating temperature, the steam discharges along with the exhaust, so as to continuously obtain qualified dry products at the bottom of the equipment. A single disk dryer can achieve the maximum heat transfer area of 400~500㎡.
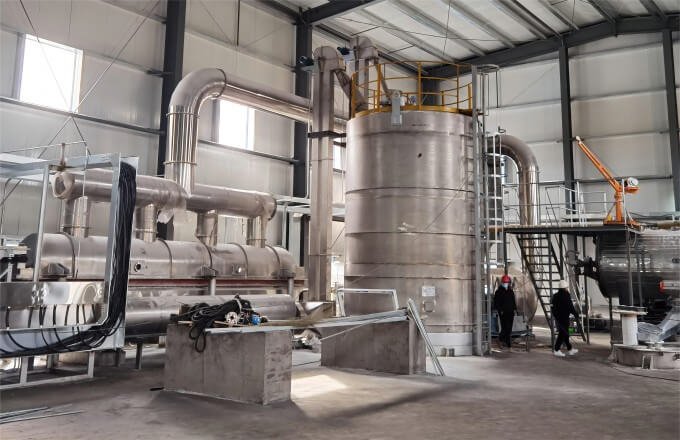
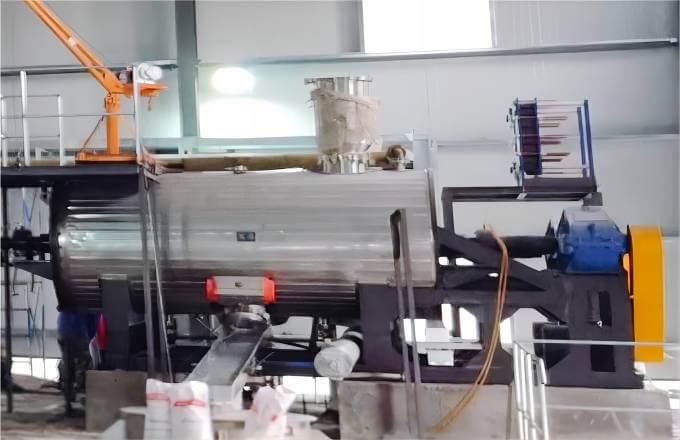
- Scraper drum dryer:
Scraper drum dryer is a drying equipment attached to the rotary drum where the liquid phase material is continuously dried through heat conduction. The liquid and the cloth device form the material film on the outer wall of the drum rotating at a certain speed, which is heated by the hot drum where the heating medium (steam or thermal oil) continuously enters. After the film is dried, it will be scraped down by the scraper.
Drum dryer is a kind of rotating drying equipment with internal heat conduction. The rotating drum adheres to a certain thickness of the material film through its bottom trough, and the heat is transported to the inner wall of the drum through the pipeline, conducting to the outer wall of the drum, to heat the film, so that the wet content in the film is evaporated, dehumidified, making the material dry. The dried material is removed from the drum by the scraper on the surface of the drum, to the screw conveyor under the scraper. And then the dry material is concentrated and packed through the screw conveyor.
- Rake Dryer:
Vacuum rake dryer is a novel horizontal intermittent vacuum drying equipment. The wet material is evaporated through conduction, with the scraper mixer constantly removes the material from the hot surface and moves on in the container, forming a circulating flow. After evaporation, the material will be drawn out by the vacuum pump.
Vacuum rake dryer is usually used for high concentration brine to reduce concentration. It has built-in scraper, to treat concentrate sticking to the wall. It is especially recommended to treat sticky or crystallized fluids, such as heavy metal wastewater, brine, mother liquid, reverse osmosis concentrated water, etc.
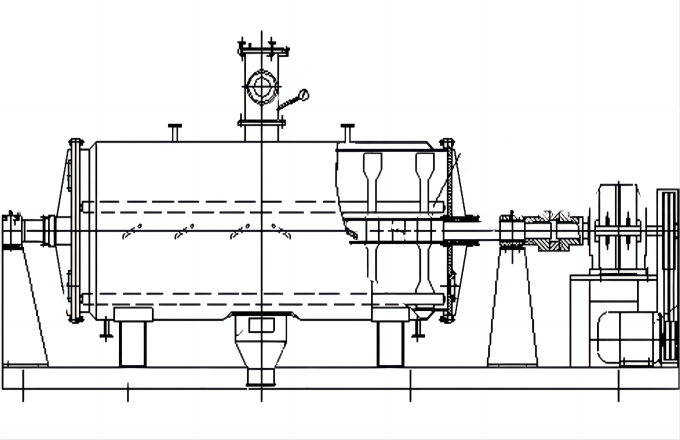
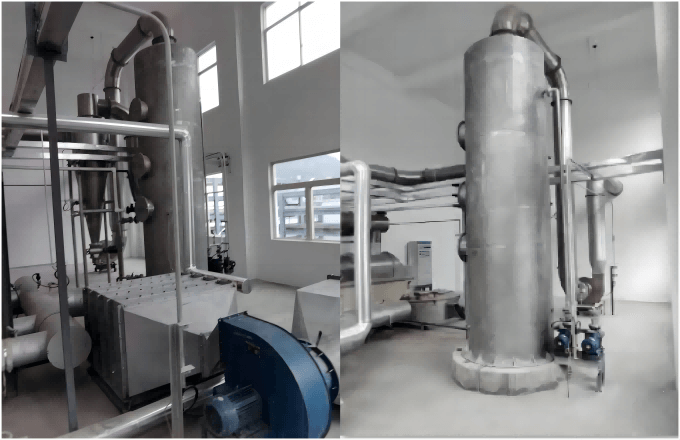
- Steam kettle drying:
When the liquid evaporates in the evaporator, the secondary steam generated is no longer used, and the liquid no longer passes into the second evaporator for concentration, that is, only one evaporator is used to complete the evaporation, which is called single-effect evaporation. The equipment using one evaporation kettle is called single steam kettle. The vacuum distillation technology is used, and the mother liquid is directly evaporated and concentrated from concentration to crystallization in a distillation kettle. This method is usually applied to MVR, or the zero liquid discharge treatment of various high-concentration wastewater, such as mother liquor discharged from multi-effect evaporation and landfill leachate.